
In 2001, a new company was established for the production of laminate flooring and MDF-HDF. The new company was a fresh player in the market, and compared to others in the industry, it aimed to diversify more (offering a wider range of products and more options) while providing better customer service (fast and reliable delivery). Additionally, the company sought to offer customized solutions, such as special laminate widths, unique designs, and more. All of this needed to be achieved at a competitive price.
To facilitate this, an entirely new plant was constructed.
This new plant consisted of three different departments:
- A department where paper was printed, which forms the design of the laminate flooring. The goal was to automatically produce both in-house designs and customer-specific designs.
- A department where the laminate boards were made. Here, the paper was applied to a base board and pressed together. Grooves could also be added to the board if needed.
- A tongue-and-groove department where the boards were cut into strips and the tongue and groove were added to the boards. After this, the laminate was packaged, with numerous packaging forms and box types available.
These three departments were connected by adding an automatic warehouse system, which was used as a storage, buffering, and transport medium.
The number of paper designs was limited, and storing paper didn’t take up much space. Therefore, it was feasible to print a larger stock of paper and store it. Similarly, the number of semi-finished products after pressing was also limited, so a decision was made to keep a sufficient stock of these as well.
However, the stock of finished products was a different matter. To maintain enough stock of every possible combination (design, width, type of tongue and groove, type of packaging, quantity per pack, stacking method, etc.) and deliver them quickly, an end warehouse of unrealistic proportions would have been needed. Such a warehouse was not economically viable. Additionally, the company wanted to avoid issues like product aging, repackaging, and damage in storage.
As a result, the decision was made to organize production differently: an automatic warehouse for semi-finished products as interim stock, paired with fast and flexible finishing lines capable of quickly and automatically producing all possible variations—a system of mass production customized to the client’s needs. The pallets coming off the line were placed in a small collection warehouse for daily production or loaded directly onto trucks for transport.
The advantages of such a system were clear: the ability to flexibly respond to customer demands, enabling special finishes, quickly adapting to trends, reliable and fast delivery, and no need for repackaging—all at a competitive price. Logistically, the company had no end stock, could avoid dead stock, and could deliver less common products just as quickly.
However, to achieve this, a production setup was needed that was fast, flexible, and fully automated. Additionally, the machines had to be able to change configurations very quickly.

Figure: Overview of the lines: The panels are cut to the correct width using an automatic saw machine and then returned to the warehouse, after which they are processed into laminate flooring via a tongue-and-groove line, a control station, and a packaging line.
The first challenge was the machines themselves. For this purpose, the various suppliers had to equip their machines with a much higher degree of automation. Almost everything that needed to be configured on the machines had to be remotely controlled, including tool changes.
The second step was adapting the ERP system. This ERP system needed to be modified to improve customer options: the ability to modify orders after they had been placed, even if production had already started, parameterizing products, entering personalized items, and providing reliable information about the status of their orders.
In addition, several essential systems were integrated into the operation: an APS (Advanced Planning System), a MES (Manufacturing Execution System) to control production, and a WMS (Warehouse Management System) for stock management.
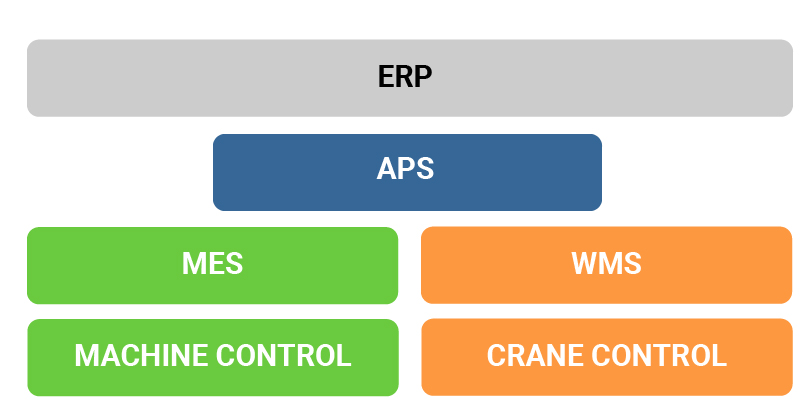
With the detailed planner, orders could be scheduled on various machines, taking into account each machine’s capabilities, promised delivery times, and the optimal sequence to minimize changeover times. Changeover times could be significantly reduced by preparing tool changes in advance.
Since the detailed planner operated in real-time, the estimated end date and time for the machines were continuously recalculated, factoring in stoppages, actual speeds, and changeover times. In case of machine downtime or breakdowns, automatic rescheduling could take place.
The semi-finished product warehouse was a large automated warehouse. The WMS (Warehouse Management System) controlled the automated warehouse. The pallets were large and heavy, which meant the response time was relatively limited. To speed up operations, optimization algorithms were developed to link this warehouse to fast production. Since the saw machine was a bottleneck, it was completely decoupled from the process.
The MES (Manufacturing Execution System) was integrated with both the detailed planner and the machines, managing the entire operation. Before starting a new order, all necessary raw materials and auxiliary products were supplied. At the start of a new order, all machine parameters were sent to the PLC (Programmable Logic Controller) to automatically set up the machine, adjust labeling, select the correct boxes, and retrieve leftover materials from the previous order.
The MES system issued an alert for any values outside the set tolerance, tracked all stoppages and reasons for downtime, as well as all reasons for second-choice products.
The result was a new automated finishing line for almost fully customized end products. All variations were processed simultaneously, and just a few minutes before completion, it was still possible to adjust the final product with different parameters.
We are on the verge of a new fourth industrial revolution, and even with today’s technology, this remains a significant challenge to achieve. However, such systems have already existed for some time.
Recent Comments